Composite packaging bags are made of two or more materials of different properties through specific processes and technologies. This kind of packaging bag combines the advantages of different materials and has excellent barrier properties, mechanical properties, heat resistance, cold resistance, oil resistance and chemical resistance.
The composite layer of composite packaging bags usually includes the following materials:
Barrier layer: such as aluminum foil, aluminized film, PET, etc., which can effectively block oxygen, water vapor and light, and protect the items in the bag from the external environment.
Structural layer: such as BOPP, PET, PA, etc., provide strength and rigidity of the packaging bag, so that the packaging bag can withstand a certain pressure and weight.
Heat sealing layer: such as LDPE, LLDPE, etc., have good heat sealing properties, ensure that the packaging bag can be tightly bonded when sealed to prevent leakage of contents.
The composite processes of composite packaging bags mainly include dry composite, wet composite, extrusion composite and co-extrusion composite. Different composite processes are suitable for different material combinations and packaging needs.
Composite packaging bags are widely used in food, medicine, daily chemicals, chemicals and other industries, especially in packaging fields that require special requirements such as high barrier properties, high temperature cooking resistance, and low temperature freezing resistance. For example, vacuum-packed food, high temperature cooking food, liquid beverages, medicines, cosmetics, etc. all require the use of composite packaging bags to ensure product quality and safety.
In addition, composite packaging bags also have good printing performance and plasticity. They can be printed with various patterns and texts according to customer needs, and made into packaging bags of various shapes and sizes to meet different packaging needs.
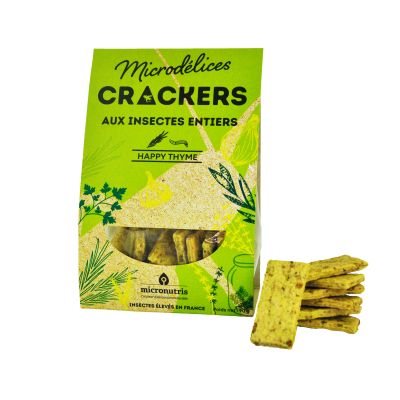